OFFICERS:
PRESIDENT:
DAVE GRAU, tictocfinewatches@verizon.net
V. PRESIDENT:
AL TAKATSCH, al_taka@yahoo.com
SECRETARY:
JOHN REILLY, jrol@aol.com
TREASURER:
STAN CRAIG, no e-mail
SERGEANT-AT-ARMS: EARL
KNIGHT, earljan@hughes.net
DIRECTORS:
JERRY KINCAID (07)
tictoctwo@aol.com
BRETT LOUIS (07)
blouis@hst.nasa.gov
DAN SPATH (07)
daspath@verizon.net
GEORGE TRESANSKY (07)
geotnant@aol.com
JACK KENNAN (08)
jgkennan@webtv.net
GEORGE PAINTER (08)
gpainter@adelphia.net
A Tribute
On behalf of the Horological
Association of Maryland, I would like to thank John Reilly for all of his hard work, dedication, and committed efforts to
help make HAM such a terrific club. John was our President and also our Secretary,
doing a phenomenal job in both roles. He led meetings, as President, in a way
that I believe became the standard for how our business meetings should be conducted.
As Secretary, John handled many of our interactions with AWCI, took great minutes, and put together a terrific newsletter.
John has been my mentor this past year. He was my go-to person for topics for meeting agendas, how to discuss certain issues
with the club, and often provided gentle prodding to make sure that I wrote my “Message from the President” by
the deadline for publication of the newsletter.
I will miss John. We will miss John.
John, as you hitch the wagon
to ride West we wish you the best that life has to offer—good health, happiness, and great joy for you and your family.
Fair seas and following winds,
my friend. Our friend. Don’t
forget us, as we will not forget you.
All our best—
The Members of the Horological Association of Maryland
****************
Secretary’s Report:
At our last workshop Bob Rothen gave part two of his talk on the lathe. A lively discussion of lathe motors, DC vs. AC current, torque and speed controls
ensued, after which Bob drew the 4 types of gravers most commonly used and another discussion of high speed steel vs. carbide
and the pros and cons of each ensued along with talk of sharpening stones and wheels.
George Tresansky told us of his best source of graving tool steel. The name of the company is International Carbide and the link is http://www.icctool.com/. After the talk we all began to make shavings or chips with lots of good ideas and information coming from our more
experienced lathers (if that’s a word).
Either e-mail or bring your ballot to the next meeting. Dan Spath will come prepared to swear-in the new officers and directors.
See you Nov. 5, 7:30 PM. John
*********************
VP
Report
Here are some pictures from our last Workshop for the Watchmaker Lathe.
Also:
Its
that time of year again where we need to vote for our favorite club officers. The Ballot below can be copied and
printed and brought to our next meeting. John Reilly will be collecting and counting them.
*******************
Horological Association of Maryland Officers and Board of Directors Ballot 2007-2008
Officers: Vote for One, for each Officer
President: David Grau
Vice President: Al Takatsch
Secretary: Dave Hannemann
Sargent-at-Arms: Earl Knight
Tresurer: Stan Craig
Write in Vote:
Board of Directors: 2 Year Term, Vote for Two:
George Painter
George Tresansky
Write in:
Bring or send to John Reilly at the next meeting.
****************
******************
Tech
Article from NOTES FROM
THE BENCH
Clock Repair Archive - - Calculating pendulum length from error in
time keeping : George T. - This ones for you!
To calculate the required length for a pendulum you can use this formula:
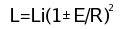
where Li is the incorrect length, L is the correct length, E is the error in timekeeping, and R is the length of the test
run. Use + if the timekeeping is fast and - if the timekeeping is slow. This is an approximate formula and the results will
be as good as your measurments and mathematics. Unfortuantely it is not possible to get an exact answer; but what you will
get will be close enough to allow for regulation.
Be sure your error E and length of test run R are in the same units.
For example if the clock is 1 minute slow in 3 days you will need to convert the days to minutes or the minutes to fractions
of a day before you plug the values into the formula.
Clock Repair Archive - - Bushings:
BUSHINGS: Bushings are part of the "bearings" of clock mechanisms. They are extremely important. Clock
brass is not all the same. It is important to realize how many different types of clocks there are in existance , and how
many have been made in the last 200 years. There are literally millions of them. Thousands of different types; made of many
different types of brass. Brass is an alloy. It is unusual in that it gets harder when struck. If you stretch a piece of soft
brass it will harden. If you hammer on a brass plate it will harden. It is important to know this when considering bushings.
Usually a bushing is not as hard as the steel of the pivot that rides in it. If the brass in a bushing is harder that the
steel in a pivot , the pivot will wear and eventually break , or stop the clock or both. If bushings have been punched the
brass will be harder. Usually this is not a problem. Sometimes the area that was punched is uneven enough to cause abnormal
wear in a pivot. Be aware of this when you check out a mechanism. Also keep in mind that many clocks were repaired during
wartime when brass and copper were used for bullets, so none was available to make clock bushings. If you wanted to fix a
clock you used a punch. There are hole closing punches available that will do an almost acceptable job but I cannot in good
conscience recommend them. If you can , use bronze bushings. Bronze bushings will outlast brass in most cases. Be sure to
check for wear that does not show: that is , wear underneath the oil cup. Before pressing in a new bushing be absolutely sure
that the hole is re-centered. Reamers are available that will make a hole just the right size for the bushing to be press-fit
into the plate. I have used a drill press to push the bushings into the plate. You must be careful not to start them crooked
or you will ruin the bushing and possibly the plate. Bushing machines are available at considerable cost. I never did use
one but I am sure they work just fine. It is my personal opinion that using a drill press is faster, but that depends on what
you are used to I am sure. I have always used a micrometer to measure the pivot sizes and it seems to work just fine. Remember
that when a bushing is pressed into the brass plate, the hole in the center of the bushing will be squeezed to a smaller size,
Between .001 and .002 is common. Keep this in mind when choosing the bushing size for the pivot. Relocating a worn bushing
to its true center is difficult and must be done carefully. Before disassembling the mechanism, after cleaning it, check each
bushing to find out how much wear has occurred. The bushings that are worn should be marked, if necessary , and the amount
and direction of wear should be noted , by a mark on the plate with a non-permanent marking pen with an extremely fine point.
With an eye loop you can see on the inside where and how the bushing has worn and with practice and time you will be able
to tell very accurately where to put the new bushing. It took me several years before I got fast at doing that. It can be
done, however, and once you catch on it will be second nature and you will be able to fit new bushings very quickly. I belive
it is possible to be more accurate sooner in your career by using a bushing machine , so if you have any doubts , maybe an
investment in one would be a good idea. They are quite expensive so be prepared to spend a lot. I have used a small round
taper file to back file the bushings to their original center. You can tell where the original center is by looking closely
at the "good" part of the busing and measuring with the micrometer to what is the center. Then file the good part to make
up for the wear pattern. Do this by filing back as far as they have worn. Then use a drill bit to open up the hole before
using the reamer on it. After pressing the bushings in you may need to ream them out to fit the pivots. Be sure you have polished
and cleaned the pivots before you fit them to the bushings. Depending on the type of clock you are working on the tolerance
will be different for the amount of play needed in the bushings. French clocks have very close tolerances .001 inch is not
uncommon. American time and strike clocks usually like to be somewhat looser. .003 thousandths is typical on the number 2
wheel time or strike. This of course also depends on the size of the pivot. On a small escape wheel three thousandths would
be too loose.
Copyright (c) 2002 David Tarsi. Permission is granted to copy, distribute and/or modify this document
under the terms of the GNU Free Documentation License, Version 1.1 or any later version published by the Free Software Foundation
*******************
HAM Meeting
Dates
November 5, Business & Continued Lathe Workshop
Nevember 26, Workshop
December Board of Directors Meeting Only